Aug 30, 2022
How Wenn Disrupts the Car Rental Industry With Make
Learn how Norwegian fintech company Wenn has unlocked new value props for car rental companies, insurance providers, and auto repair shops to detect damages and remove friction in the handling process.
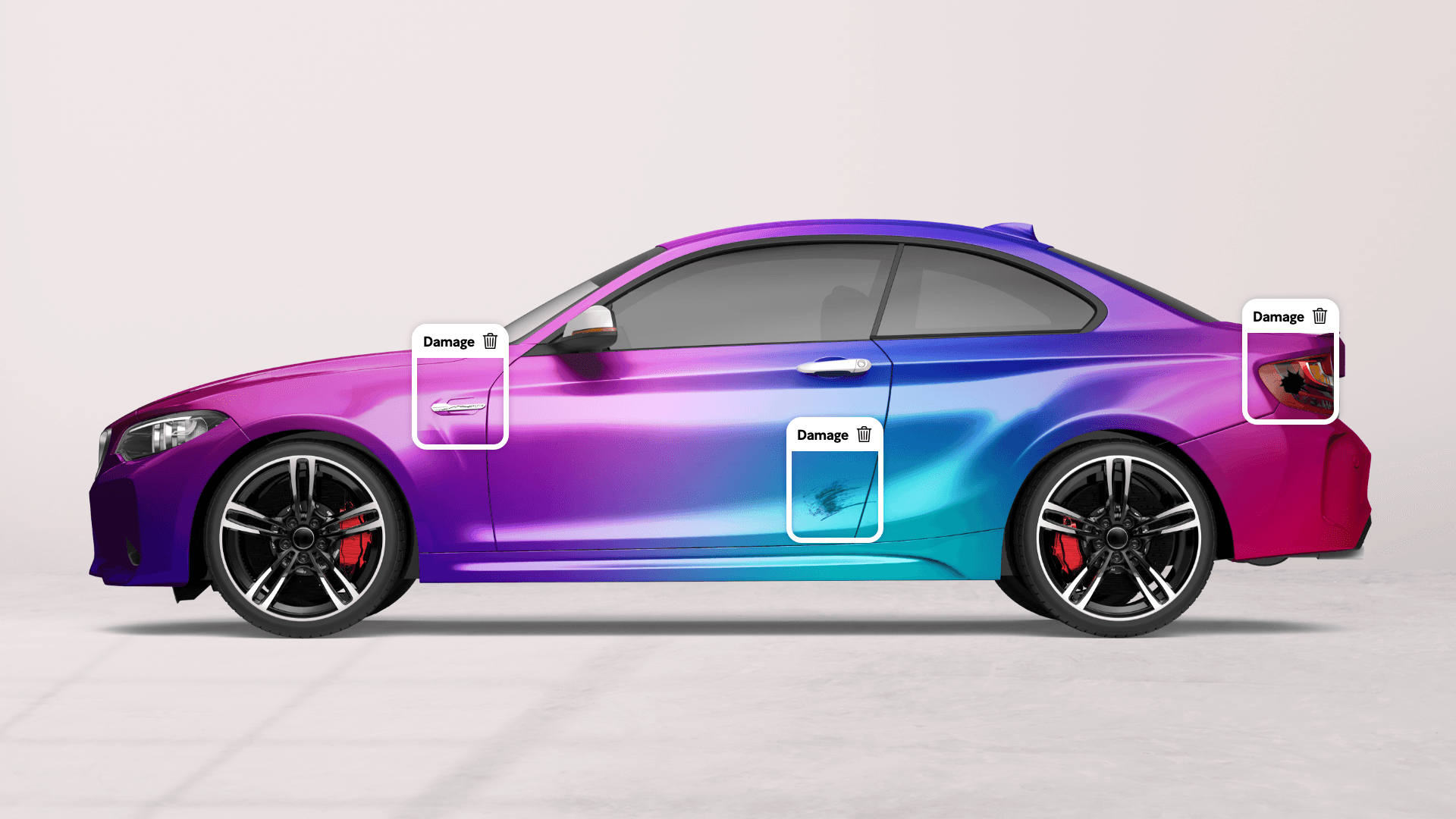
Anyone who’s ever rented a car knows how cumbersome and stressful it can be to return it.
Usually, you have to show up with the car at a specific location (such as an airport), wait for someone from the rental company to check for damages, and - if all is good - sign some paperwork before you can continue your journey.
This experience can get even worse if you’re returning a car during peak rush hour (as you’ll have to wait longer for the car to be inspected), or if some damage is found in the unit you’re returning.
At this point, disagreements and confrontations are not at all rare.
Rental car companies aren’t particularly happy about the current car handling process either, as it demands too much manual work (inspectors) and unbalanced workloads (rush hours).
Moreover, inspectors often miss damage made to cars. Whether due to pressure during peak hours, the lack of adequate tools, or just misplaced attention, this common human error translates into bottom-line losses.
That is exactly what Norwegian fintech company Wenn saw before coming up with an innovative solution that is revolutionizing damage detection processes for car rental companies.
Let’s take a closer look at their solution, and the role Make plays in what we believe will become the new benchmark for damage detection and damage handling in the years to come.
Wenn’s sweet spot: Fast, but not furious
Seeing the long-lasting issues in damage detection processes, Wenn came up with a logical, and yet unseen solution to accurately scan and detect damages as fast as possible: Automated car scanners (aka “CarEye® Capture”) located in busy hubs where people return their rental cars.
Wenn’s capture devices can detect car damages in seconds, but they soon encountered a roadblock to achieving maximum efficiency: The lack of a robust central system to monitor, process, and analyze data in real-time.
In other words, the capture devices were fantastic, but the capability to transform the resulting rig data into actionable analytics and reports for all stakeholders (Wenn, rental car companies, end customers) was missing.
On top of this, Wenn required a solution to remotely monitor multiple capture devices distributed across several locations.
At this stage, Wenn considered several alternatives (including Zapier) to fill the gaps, but ultimately chose the platform that allows anyone to visually create and develop logical business flows at speed: Make.
Building an end-to-end logging and monitoring solution in a matter of weeks
After onboarding Make, Wenn started to design, build, and automate workflows with ease.
Their first move was to combine scan and detection data from a few cars into a single dashboard.
This led to more advanced analysis, and the power of pushing real-time data through Make was discovered.
Important rig health metrics such as CPU temperature, camera quality, and the time it takes cars to pass through each damage detection checkpoint were made available in a flexible dashboard in just a few simple clicks.
Wenn didn’t stop there, and took its monitoring solution to the next level by setting up alerts and triggers that give them complete control over the state of its capture devices and daily operations.
In just a few weeks, Wenn was able to build a comprehensive logging and monitoring solution with a detailed view of its entire customer lifecycle and business operations.
Or as Wenn’s CTO Gian Kolbjørnsen puts it: “Make has made it possible for us to monitor our whole pipeline - from high-tech AI edge device to cloud solution - in a pipeline that is constantly evolving with very high complexity and very high amount of data”.
The result: A new value proposition for car rental companies
Wenn’s solutions are already producing staggering results for car rental companies.
At Norways’ Gardermoen airport alone, Wenn scans 1,000 cars daily and generates over 300,000 images per week.
Other airports are quickly taking notice.
A new project in Munich will see a car scanned every 6 seconds. This represents the fastest, most accurate car damage detection process in history.
Within minutes of scanning a car, Wenn automatically sends a detailed report to their customers, highlighting any new damages and the time the vehicle was returned.
This rapid turnaround time is not matched by anyone else in the market.
This changes the game for car rental companies, giving them room to charge customers for late returns, preventing the manual inspection of thousands of cars each day, and saving hundreds of hours in resources.
On top of this, Wenn’s cutting-edge tech is so powerful that it can identify car damages not visible to the human eye, helping car rental companies accurately assign dents to the correct driver of the vehicle.
This adds a much-needed “fairness” factor, giving drivers the peace of mind that they won't be charged for damages they didn't cause - and thus, avoiding nasty, unnecessary confrontations.
Final thoughts
In a few weeks, Wenn built a robust logging and monitoring solution to manage its entire customer pipeline with Make.
"I wouldn't make the integration anywhere else, it would be too time-consuming to write the code and do it when you can just create the integration with Make in a few clicks and have a stable solution,” says Gian Kolbjørnsen.
Wenn has unlocked new value props for customers, disrupting how car rental companies, insurance providers, and auto repair shops detect damages and remove friction in the handling process.
If you are curious and want to learn more about Make and how it can support your growing business, reach out to one of our account executives.
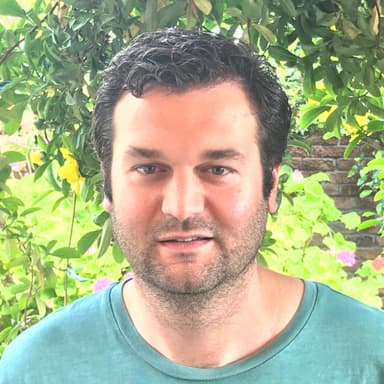
Dean Maree
Product Marketing Manager at Make. Passionate about tech and B2B product marketing. A sports enthusiast that also enjoys a run in the forest or a relaxing day out at the beach.